Dry and wet mix process shotcreting
- Theory
- Possibilities
- FAQ
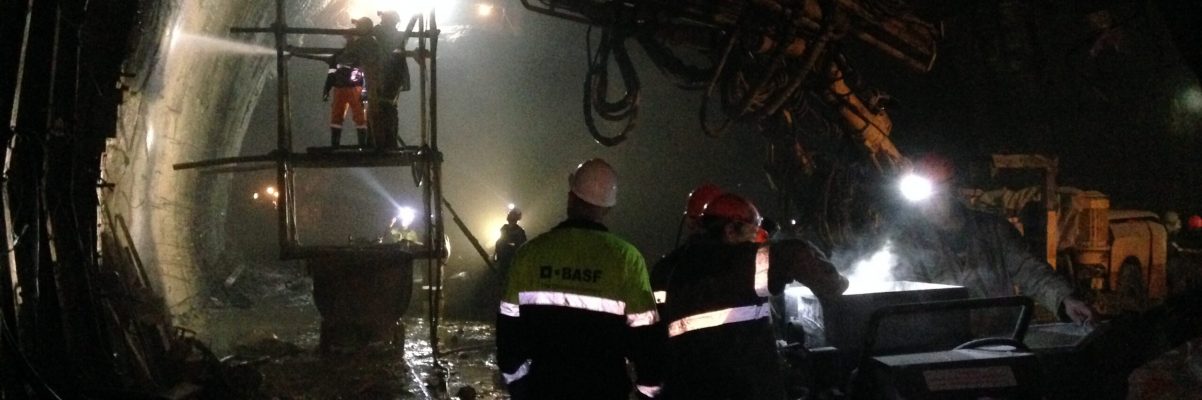
There are two methods of shotcreting: dry and wet mix process shotcreting. The wet mix process, in turn, is subdivided into continuous flow process and discontinuous flow process. Each of these methods has its own advantages and disadvantages.
Dry mix shotcreting
Dry mix process shotcreting (gunite) was first used in the early twentieth century. In this method, a dry mixture of cement, aggregates (sand, crushed stone) and additives (if necessary) is prepared beforehand. The mixture is fed into the dry mix shotcrete machine. Compressed air is fed through a hose to the nozzle, the mixture is mixed with water that is fed by another hose, and at high speed (130–170 m / s) is sprayed on the shotcreted surface.
The process of building up the shotcrete layer is performed in the following way:
- in the first period (measured in milliseconds) almost all the mixture bounces off the surface; only the cement milk clings on the surface, creating the adhesive layer;
- in the next instant, the smallest aggregate sticks to the surface, and everything else bounces off;
- progressively, larger and larger aggregate pieces remain on the surface until the rebound becomes stable.
The resulting layer of shotcrete has the following advantageous properties determined by the application method:
- high adhesion as a result of the fact that the boundary layer is formed by the cement milk with the finest aggregate;
- high density and cohesion due to the high speed of the mixture particles: the particles are literally hammered into the existing layer of shotcrete;
- optimal water-cement ratio – an experienced will ensure the amount of water does not exceeed that required for the hydration reaction;
- possibility of applying a layer of up to 10-15 cm in one work run – high consistency of the applied mixture: all that is badly fixed rebounds.
However, up to 25% of the mixture is lost due to rebound.
Wet mix continuous flow process shotcreting
Wet mix shotcreting was introduced half a century later. It was primarily due to the development of construction chemistry. According to this method, the ready concrete mixture is fed into the wet shotcreting machine (concrete pump) and hydraulically (in a continuous flow) is fed through a hose to the nozzle. Another hose supplies the nozzle with compressed air, which breaks the continuous flow of mixture and delivers it to the shotcreted surface . The speed of shotcreting for this method is significantly lower. As a result, the amount of rebound is reduced by up to 10%.
The high quality of shotcrete is achieved by using additives.
- adhesion with the surface is achieved by means of forced application of the adhesive layer;
- application of a thick layer is reached by adding a solution of setting accelerants that is supplied to the nozzle by a separate hose;
- optimal water-cement ratio is possible due to using plasticizers.
Wet mix process shotcreting is more in line with the industrial method of construction. Concrete mixture can be prepared at a specialized enterprise (concrete plant), delivered by a concrete mixer truck and the qualification of the nozzleman plays less of a role during its application.
However, the need of additives significantly increases the cost of the mixture applied. In addition, the flow of the mixed concrete by hose excludes the possibility of even short-term interruptions during shotcreting without the need to perform the time-consuming operation of flushing the hose (as concrete mixture sets in the hose).
Wet mix discontinuous flow process shotcreting
According to this method, the ready-made concrete mixture is fed into the pneumatic concrete pump and, using compressed air, is delivered to the nozzle where it is sprayed at high speed onto the surface. This method falls in between the gunite and wet mix continuous flow methods. It provides for a possibility of preparing the ready mixture at the concrete plant and there is no need to add plasticizers to it.
The disadvantages of this method include a high rebound of up to 25%, the need to apply an adhesive layer, the use of accelerants, and the necessary washing of the material hose during breaks in the work.
- Theory
- Possibilities

Stages and shotcreting cost in the repair of reinforced concrete structures by shotcreting
- Cases
- Theory
- Possibilities
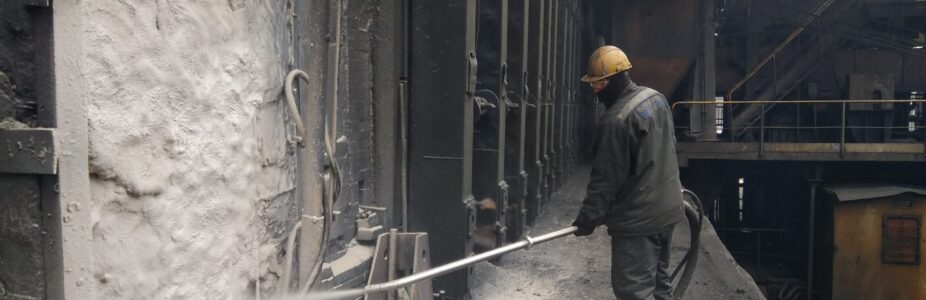
Repairing reinforced concrete structures: types and restoration options
- Theory
- FAQ
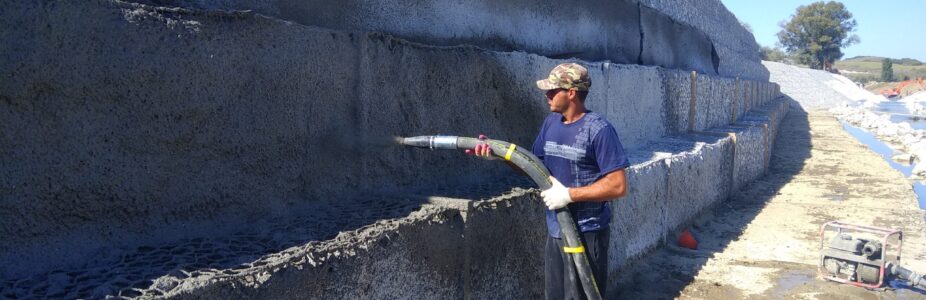
Dry-mix and wet-mix shotcreting: comparison and applications
- Theory
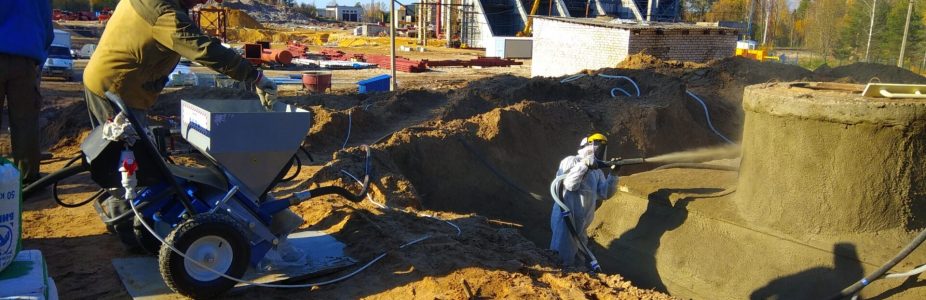
Dictionary of shotcrete terms
- Economics
- Theory
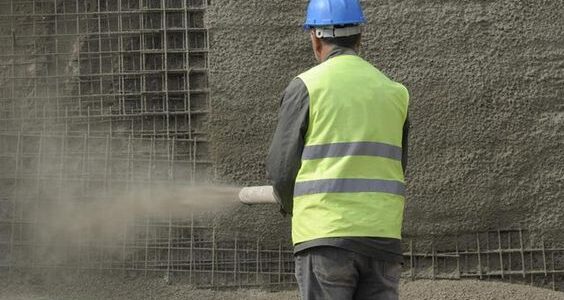